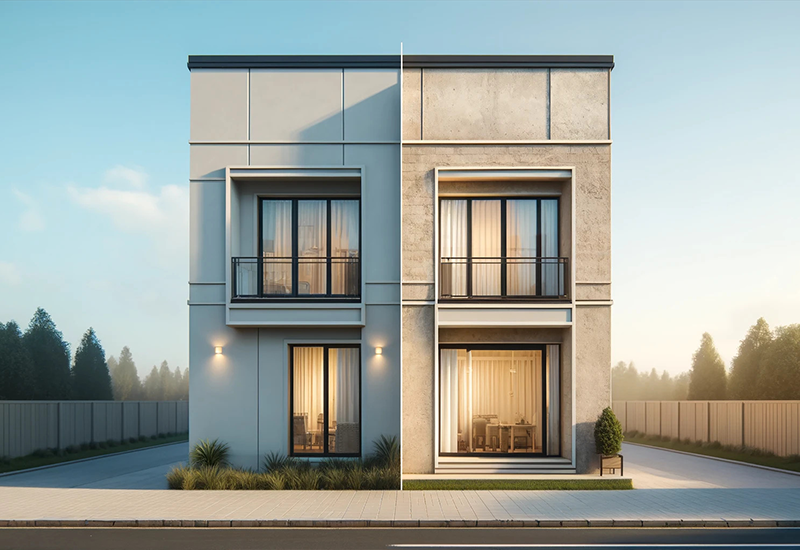
When choosing between EIFS vs stucco for your building’s exterior, understanding the key differences can guide your decision. Both EIFS vs stucco offer unique benefits and features that suit various architectural styles and climates. This comparison explores the durability, cost-effectiveness, and aesthetic versatility of EIFS vs stucco, providing insights to help you select the best option for your project.
Table of Contents
What is EIFS?
EIFS stands for Exterior Insulation and Finish Systems, a sophisticated cladding system widely used in modern architecture. This technology serves not only as external wall insulation but also as an aesthetic finish to buildings, offering a range of textures and colors. The unique layering of EIFS provides superior energy efficiency, helping buildings stay warmer in the winter and cooler in the summer, which can lead to significant savings on heating and cooling costs.
EIFS consists of multiple layers, each with a specific function, starting from a foam insulation board attached to the exterior wall, followed by a base coat that embeds a mesh for added durability, and finishing with a versatile color and texture coat that provides both style and resistance to weather conditions. This combination makes EIFS an attractive option for both new constructions and renovations seeking improved thermal insulation and a modern look.
Components
The structure of EIFS includes three critical components:
- Insulation Board: This layer is typically made from expanded polystyrene (EPS), and it is affixed directly to the exterior wall surface. It plays a crucial role in reducing energy loss.
- Base Coat: Over the insulation, a polymer-modified cement base coat is applied. This layer embeds a fiberglass mesh that provides strength and durability to the system.
- Finish Coat: The outermost layer of EIFS, the finish coat, is what is visible to the eye. It can be customized with various textures and colors, and it serves to protect the underlying layers from weather elements while also beautifying the building’s exterior.
History and Evolution
Originally developed in Europe after World War II to insulate aging buildings, EIFS was introduced to the American market in the 1960s, primarily for commercial applications. Since then, it has evolved significantly. Initially, EIFS were simple barrier systems that did not account for moisture management. However, following challenges related to moisture, newer systems include a drainage layer that helps prevent water accumulation, enhancing the durability and integrity of the system.
The advancement of EIFS over the years has focused on improving the material’s flexibility, durability, and moisture management capabilities. Today, EIFS is not only used for its functional benefits but also for its aesthetic versatility, allowing architects and builders to achieve a variety of looks ranging from smooth and sleek to textured and richly detailed.
What is Stucco?
Stucco is a time-tested cladding material made from mixing cement, sand, lime, and water. It’s renowned for its robustness and texture, which can be crafted to suit various architectural styles. This plaster has been used for centuries to coat and protect exterior walls, providing not just a shield against the elements but also enhancing a building’s aesthetic appeal.
Composition
The composition of stucco is fairly straightforward yet highly effective:
- Cement forms the base of the mixture, offering durability and a solid structure.
- Sand adds strength and bulk to the cement, helping to prevent cracks.
- Lime increases the elasticity and workability of the mixture, which makes it easier to apply and reduces the risk of crumbling.
- Water activates the cement and lime, allowing them to chemically bond and harden over time.
Together, these ingredients create a versatile and durable material that adheres well to different surfaces, including brick, stone, and wood framing.
Application Process
The application of stucco involves several steps that must be carefully followed to ensure the best results:
- Preparation of the Surface: The wall must be clean and rough enough to allow the stucco to adhere properly. This might involve applying a water-resistant barrier and a metal lath (wire mesh) over the surface to provide a good base for the stucco.
- Mixing: The components are mixed together to form a paste. Consistency is key here; the mix must be workable but not too wet.
- Application: Stucco is typically applied in three layers:
- Scratch Coat: The first layer is applied and then scratched with a trowel to create a rough surface, which helps the next layer adhere better.
- Brown Coat: The second layer is applied over the scratch coat to even out the surface and provide additional strength.
- Finish Coat: The final layer, which can be textured and colored as desired to achieve the specific look of the building.
- Curing: Stucco must be kept moist and allowed to cure slowly to prevent cracking. This process can take several days, depending on the climate and the composition of the stucco.
This methodical application ensures stucco not only adds a protective layer but also enhances the building’s insulation properties, making it a practical choice in various climates. By using stucco, builders can achieve a finish that not only looks great but also stands up to the test of time, making it a favored choice for many residential and commercial properties.
Performance and Durability
When selecting a wall finishing system, understanding the performance and durability of available options is crucial. Let’s dive into how EIFS and stucco compare in terms of insulation, resistance to weather conditions, and overall longevity.
Insulation and Energy Efficiency
EIFS are renowned for their superior insulation properties. The core of any EIFS is its thick layer of insulation, typically made of expanded polystyrene or similar materials. This insulation layer significantly reduces thermal bridging through the building’s exterior, making EIFS highly energy efficient. In contrast, traditional stucco provides some insulation but not to the extent of EIFS. Stucco’s primary materials—cement, sand, and lime—do not inherently offer the same level of thermal resistance. Consequently, buildings with EIFS tend to have lower energy costs due to better heat retention in winter and a cooler interior during summer months.
Resistance to Weather Conditions
Both EIFS and stucco are designed to withstand various weather conditions, but they do so in different ways. EIFS includes a finish that is both flexible and water-resistant, which can adapt to changes in temperature without cracking as easily as stucco might. Modern EIFS systems also include drainage capabilities that prevent water accumulation, a crucial feature in areas with heavy rainfall. On the other hand, while stucco is inherently tough and durable, it is more susceptible to cracking due to its rigid nature, especially in climates with frequent temperature fluctuations. Both materials, however, require proper installation and maintenance to maximize their resistance to environmental stresses.
Longevity and Durability Concerns
EIFS, when correctly installed and maintained, can last as long as any high-quality stucco finish. Common concerns with EIFS involve improper installation leading to moisture intrusion, which can cause structural damage over time. Stucco, meanwhile, is prone to cracking as it ages, which can also lead to water issues if not addressed promptly. Both materials are durable, but their longevity largely depends on factors such as the quality of installation, ongoing maintenance, and local climate conditions. Regular inspections and prompt repairs are vital to extend the life of both EIFS and stucco finishes.
By understanding these aspects, homeowners and builders can make more informed decisions based on their specific needs, ensuring they choose a material that not only enhances the building’s appearance but also provides long-term durability and performance.
Aesthetic and Design Flexibility
Choosing between EIFS and stucco often comes down to considering their aesthetic and design flexibility. Each offers unique possibilities that can significantly impact the overall look and feel of a building.
Texture and Color Options
EIFS offers remarkable versatility in both texture and color. Because you can customize the outermost layer of EIFS, which is a finish coat, it allows for a wide range of textures—from smooth to heavily textured—mimicking other materials like stone or wood. You can mix the finish coat with different pigments, making the color options virtually limitless. This adaptability makes EIFS an excellent choice for projects where creative expression and specific design intents are prioritized.
On the other hand, stucco might seem a bit more limited in terms of texture but still offers a considerable range of possibilities. It can be finished in various ways to create different textures such as smooth, raked, or even an artistic pattern. The mix gives stucco its coloration, or you can achieve it by painting the dried surface. This method does not provide as much flexibility as EIFS but still offers a range of options suitable for many design needs.
Architectural Suitability
When it comes to architectural suitability, EIFS and stucco cater to different types of buildings and styles. Its smooth finishes and sharp, clean lines make EIFS particularly suited for modern and contemporary architectures. Builders and architects can easily shape and mold it, which is ideal for buildings with intricate designs and unique architectural features. Additionally, its lightweight nature makes it suitable for high-rise buildings where heavy claddings may pose structural challenges.
Stucco, with its traditional appeal, is often the go-to choice for Mediterranean, Spanish, or Colonial-style buildings. Many historical and residential structures favor its texture, providing a classic look. Stucco’s robustness and the tactile quality of its finish lend an ageless charm, making it ideal for projects that aim to reflect a sense of timelessness and durability.
Installation Techniques and Maintenance
The installation and maintenance of EIFS and stucco are critical factors to consider, as they significantly impact the longevity and performance of these materials. Proper installation by trained professionals and regular maintenance can make all the difference in ensuring these finishes look great and function effectively for years to come.
Professional Requirements for Installation
Installing EIFS requires a specific skill set and knowledge, as it involves several layers and precise techniques to ensure proper insulation and moisture control. Professionals installing EIFS must be certified, which involves training on the correct application methods and understanding the technical aspects of the EIFS system, including its drainage capabilities. This certification ensures that installers meet high standards when installing EIFS, preventing future problems such as moisture accumulation or thermal inefficiencies.
Stucco installation, while also demanding professional expertise, does not typically require specific certification. However, it requires skilled craftsmen familiar with mixing and applying the material to achieve the desired durability and appearance. Craftsmen have refined the application of stucco over centuries, requiring a thorough understanding of the materials and techniques to ensure a finish that is not only aesthetically pleasing but also stands up to environmental stresses.
Ongoing Maintenance Demands
Once installed, both EIFS and stucco require ongoing maintenance, though the nature and frequency of this maintenance can differ significantly between the two.
- EIFS Maintenance: You need to inspect EIFS regularly for any signs of damage or wear, particularly around windows and doors where sealant may fail and allow water ingress. It’s also important to ensure that the EIFS surface is clean and free from debris that can retain moisture. Despite these needs, EIFS generally requires less frequent painting or color touch-ups compared to stucco, as the color and texture are integral to the finish coat.
- Stucco Maintenance: Stucco may require more frequent maintenance, depending on the climate and exposure conditions. This includes periodic painting or sealing to maintain its color and protect it from moisture penetration. Settling or seismic activity can cause stucco to crack, so you need to promptly repair these cracks to prevent water damage and further deterioration.
Both materials benefit greatly from routine inspections and timely repairs, ensuring they continue to protect and enhance the building effectively. By understanding these requirements, property owners can plan for the ongoing care needed to maintain the aesthetic and structural integrity of their EIFS or stucco finishes, thus maximizing their investment.
Cost Analysis
Evaluating the cost implications of EIFS versus stucco involves looking at both the initial installation costs and the long-term financial benefits. Understanding these costs can help property owners make an informed decision based on both upfront investment and potential savings over time.
Initial Installation Cost
The cost of installing EIFS generally tends to be higher than that of stucco. This is largely due to the materials used and the complexity of the EIFS system, which requires specialized labor and additional components for proper installation. Below is a table that provides a comparative overview of average installation costs per square foot for both materials:
Material | Average Cost per Square Foot |
EIFS | $10 to $15 |
Stucco | $6 to $9 |
These prices can vary based on regional labor costs, the complexity of the project, and the quality of materials used. EIFS might require additional costs related to ensuring proper moisture barriers and drainage systems are in place.
Long-term Financial Benefits
While EIFS has a higher initial cost, the long-term savings can be substantial, primarily due to its superior insulation properties. Buildings with EIFS tend to have lower heating and cooling costs, which can result in significant energy savings over time. Additionally, EIFS can have lower maintenance costs compared to stucco, as it does not require frequent repainting or crack repairs.
Stucco, while less expensive initially, may lead to higher long-term costs due to its need for periodic maintenance like painting and crack filling to maintain its aesthetic and functional integrity. However, stucco’s durability and time-tested performance also mean it can be a cost-effective option if maintained properly.
Here’s a breakdown of potential savings from energy efficiency:
Material | Estimated Annual Energy Savings |
EIFS | Up to 20% reduction in energy costs |
Stucco | Less energy savings potential |
These savings are based on average energy costs and can vary by climate and individual building characteristics.
Environmental Impact and Sustainability
When selecting building materials like EIFS and stucco, considering their environmental impact is crucial. This involves looking at how these materials are produced and what happens when they are no longer in use.
Material Production
- EIFS: Manufacturers produce EIFS components using several synthetic materials, including polymers and adhesives derived from petroleum-based products. While the manufacturing process of EIFS is relatively energy-intensive, the product’s superior insulation properties can offset these initial environmental costs by reducing the energy needed to heat and cool buildings. Additionally, manufacturers have made strides in making the production process more environmentally friendly. This is done by integrating recycled materials and improving the efficiency of the manufacturing processes.
- Stucco: On the other hand, stucco’s primary components—cement, sand, and lime—are natural and abundant. The production of cement, however, is energy-intensive and generates significant amounts of CO2. Despite this, stucco’s long lifespan and minimal maintenance requirements contribute positively to its environmental profile. This reduces the need for frequent replacements or repairs.
End-of-Life Recycling and Disposal
- EIFS: Disposal and recycling of EIFS can be challenging due to its composite nature. The layers of synthetic materials and adhesives can make it difficult to recycle in a conventional sense. However, you can grind down some components of EIFS and reuse them in other applications, although widespread recycling programs for EIFS are not yet common.
- Stucco: Natural, inert, and non-toxic minerals primarily compose stucco, making it more straightforward to dispose of at the end of its life. You can often crush and recycle it as aggregate in new construction materials or safely dispose of it in landfills without leaching harmful chemicals.
In both cases, the environmental impact is significant but you can mitigate it by considering the full lifecycle of the materials. We encourage manufacturers and builders to follow sustainable practices, such as using recycled materials and minimizing waste during installation, to improve the overall sustainability profile of their projects. Understanding these environmental considerations enables builders and homeowners to make more informed choices aligning with their sustainability goals. This contributes to a more eco-friendly construction industry.
Common Misconceptions
Understanding the myths and misconceptions surrounding EIFS and stucco is vital for making informed decisions about these materials. Let’s debunk some of the most common misunderstandings to ensure clarity and confidence in their use.
Myths about EIFS
Myth 1: EIFS Traps Moisture
One of the most prevalent misconceptions about EIFS is that it inherently traps moisture, leading to mold and structural damage. However, designers equip modern EIFS with advanced moisture management systems that include a drainage plane. These systems effectively channel water away from the wall assembly, preventing moisture buildup when installed correctly.
Myth 2: EIFS is Not Durable
Some believe EIFS is less durable than other cladding options. In reality, EIFS offers excellent durability when properly maintained and inspected. Designers have made it to withstand wind and thermal expansion. If the system includes proper detailing around openings and edges, it can last as long as any high-quality cladding system.
Myth 3: EIFS is Only for Commercial Buildings
Although builders initially used EIFS more commonly in commercial construction. Its energy efficiency and versatility in finishes are making it increasingly popular in residential projects. Designers can tailor it to fit any architectural style, proving its versatility beyond commercial applications.
Stucco Myths Debunked
Myth 1: Stucco is High Maintenance
Many assume stucco requires high maintenance. While stucco does require some upkeep, such as occasional cleaning and crack repair, these maintenance requirements are not overly burdensome compared to other siding materials. Regular inspections can prevent minor issues from becoming major problems, making stucco a relatively low-maintenance option.
Myth 2: Stucco is Only Suitable for Warm Climates
People have stereotyped stucco as a material only suitable for warm, dry climates like those found in the Mediterranean or southwestern United States. However, with the right installation techniques and materials, including proper barriers and insulation. Builders can use modern stucco systems effectively in a variety of climates to prevent moisture penetration and manage thermal performance.
Myth 3: Stucco Easily Cracks and Crumbles
Another common myth is that stucco is prone to cracking and crumbling. While stucco can develop cracks due to settling or seismic activity, these issues are manageable through proper application and periodic maintenance. Using reinforcing mesh and control joints during installation can greatly reduce the risk of significant cracking.
By clearing up these misconceptions, homeowners, builders, and designers can better appreciate the benefits and proper uses of EIFS and stucco. This ensures that decisions are based on facts rather than myths. This knowledge helps in choosing the right material for specific project needs. It also aids in implementing best practices for installation and maintenance.
Conclusion
Choosing between EIFS vs stucco depends on your specific needs and preferences. EIFS offers excellent insulation and design flexibility. Stucco provides a classic aesthetic and has been a reliable choice for many years. If you are seeking professional installation for EIFS vs stucco, consider reaching out to experienced contractors. They can provide detailed insights and quality service. For professional inquiries, please contact +(1) 917-477-9667 to find the right contractor for your EIFS vs stucco needs.
FAQs
Q: What are the main differences between EIFS vs stucco?
A: The main differences between EIFS vs stucco lie in their composition and insulation properties. EIFS offers superior insulation and greater versatility in finish options. Architects and builders celebrate stucco for its timeless appearance and robustness.
Q: Can EIFS be as durable as stucco when exposed to harsh weather conditions?
A: Yes, when comparing EIFS vs stucco, EIFS can be as durable as stucco. It includes a proper drainage system to prevent moisture buildup, making it adaptable to a variety of climates.
Q: How does the installation cost of EIFS vs stucco compare?
A: The installation cost of EIFS vs stucco shows that EIFS tends to be more expensive initially. This is due to its complex installation process and materials. However, the energy savings from EIFS can offset the higher upfront cost over time.
Q: Which is more suitable for residential buildings, EIFS vs stucco?
A: When deciding which is more suitable for residential buildings, EIFS vs stucco, EIFS proves to be a great choice. It offers design flexibility and excellent insulation properties, ideal for both residential and commercial buildings.
Q: What are the maintenance requirements of EIFS vs stucco?
A: When discussing the maintenance requirements of EIFS vs stucco, note that stucco generally requires more upkeep. This includes regular painting and sealing to maintain its appearance and integrity.